Alex Rogo manages a failing manufacturing plant for the company UniCo in a small American town. One day, he arrives at work to find his corporate division manager, Bill Peach, waiting for him. Peach is angry about a customer order that is months overdue, as are most of the orders in Alex’s plant. He tells Alex that the outstanding order must be shipped by that evening, and that if Alex can’t turn the plant around within three months, Peach will shut it down. Alex and his production manager, Bob, manage to push everyone in the plant and fulfill the order by that night, but Alex knows that they can’t keep operating the plant in such a hectic fashion. Worse yet, Alex’s wife, Julie, wants to go out with him that evening, but Alex has to spend all evening at the plant, as he often does, which upsets her.
While at a division meeting, Alex has the sense that nobody in their division has any real idea how to successfully manage a manufacturing system. He remembers advice that an old mentor, Jonah, gave to him two weeks ago when he ran into Jonah at an airport: though they hadn’t seen each other in years, within minutes of Alex talking about the plant, Jonah intuited exactly what problems it has. Jonah advised Alex that he needs to determine the overall goal of the manufacturing plant. Now restless at the division meeting, Alex abruptly leaves to be alone and think. After several hours, he decides that the goal of any business must be to make money, and thus he can measure the productivity of any action by whether it helps the plant make money. Alex discusses this idea with Lou, his chief accountant. Lou agrees that it makes sense, but he thinks they would need particular metrics with which to measure that goal.
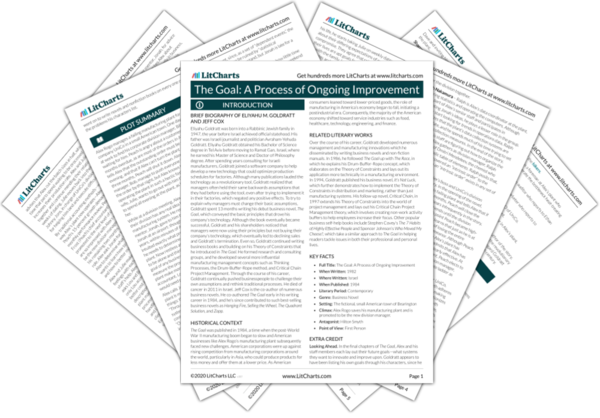
Alex calls Jonah and Jonah explains to determine whether the plant is making money, Alex only needs to measure three things: throughput, inventory, and operating expense. “Throughput” describes the money that a manufacturing system makes from sales. “Inventory” describes the money contained in that system as raw material or equipment. “Operating expense” describes the money required to turn inventory into throughput. The next day, Alex presents these new metrics to Bob, Lou, and Stacey, the plant’s inventory control manager. They discuss whether the plant’s newly-acquired robots, which are efficient in that they are always operating, actually generate more throughput or waste money by doing unnecessary work and creating unnecessary inventory. They still feel uncertain, so Alex decides to take an overnight flight to meet with Jonah and ask for advice. However, Julie is angry at Alex for his unannounced travel plans. In New York, Jonah warns Alex that a plant where everyone is always busy is a wasteful and inefficient plant at risk of going bankrupt, since, as a set of “dependent events,” the manufacturing process can be ruined by “statistical fluctuations.” Alex doesn’t understand, but Jonah is late for a meeting and leaves.
When Alex gets home, he and Julie fight about how little time he spends with her. He promises to spend the entire weekend with her, but on Saturday he realizes that he promised to go with his son, Dave, on an overnight Boy Scout hike. During the hike, Alex realizes that the hikers are a set of dependent events like stages in a manufacturing system, and each of their fluctuations in hiking speed causes compounding delays for everyone behind them in line. However, he also realizes that by placing the slowest kids at the front if the line and the fastest kids at the back, he can mitigate the amount of delays and disorder that arises.
Alex is excited about what he has learned and believes he can put it into practice at the plant. However, when he and Dave get home from the hike, he discovers that Julie has left him. He asks his mother to move in and help him take care of the kids while he deals with work and figures out where Julie went. Meanwhile, Alex observes the same compounding delays due to statistical fluctuations in the plant, even when each machine and person is individually efficient. Alex and his staff realize that they need to optimize their entire manufacturing system rather than focus on individual efficiencies. When Alex reports this to Jonah, Jonah tells him his next step is to identify the “bottlenecks” in his plant, the machines and resources that are the slowest due to their limited capacities, since these slow down the entire manufacturing system. Alex and his staff realize that they have two bottleneck machines, neither of which can be sped up, and through which most of the parts they make must go. Jonah advises that since the bottlenecks are the slowest component of the manufacturing system, if they can increase their bottlenecks’ capacity, they can increase the capacity of the entire system, which will raise their throughput. Jonah gives them advice on how they can improve the way they operate their bottlenecks to increase their capacity, and Alex and Stacey develop a tagging system to organize which parts need to be processed by bottleneck machines.
Alex finds out that Julie is living with her parents and considering divorce. To prevent this, he starts going to see her several times a week, and they even start going on dates together. Meanwhile, the plant shows real improvement by lowering its stock of excess inventory and shipping orders on time. Within two months, the plant is profitable again. Jonah teaches Alex how to let the bottleneck machines regulate the pace of the entire system and maintain a steady flow of manufactured products. However, despite their good progress, Peach is unimpressed and tells Alex that he needs to see an astronomical 15-percent improvement in their third month, or he will still close the plant. Alex is disheartened, but Jonah feels confident they can deliver. As their next major step, Jonah advises that Alex cut the batch sizes in half, which halves the time that parts spend waiting to be processed and further increases their production rate. Alex and Julie spend more time together and continue mending their relationship—after a few weeks of dating, Julie moves back into their home. Meanwhile, Johnny Jons, in charge of UniCo’s division sales, praises Alex for helping him land and execute difficult orders.
By traditional accounting methods—which don’t conform to the way Alex’s plant now operates—Alex’s plant does not meet Peach’s 15-percent growth demand. However, at Alex’s monthly performance review, Peach reveals that he, Ethan Frost (Peach’s chief accountant), and Johnny Jons are being promoted to the next level of corporate administration. They are so impressed with Alex’s work that Peach promotes Alex to be the new division manager, recommending that Alex spend his remaining two months at the plant preparing for his new role. Alex asks Jonah for help preparing, and Jonah encourages Alex to determine what he wants to learn. Alex decides that he wants to learn how to manage organizations of any size or scale and how to better manage his personal life.
Alex and Julie make an effort to share their thoughts and feelings with each other on a daily basis. Meanwhile, with his staff’s help, Alex prepares for his role as division manager. He asks Lou and Bob to move up to the division level with him, but only Lou accepts the offer. Lou states that he wants to devise better cost accounting metrics that give a more accurate description of a business’s health. Bob wants to become the plant manager in Alex’s stead and master plant-level production processes. Alex spends the next two months learning and handling minor issues at the plant. With their new capacity, Alex and Lou help Johnny Jons land a contract with a large French client, helping their company make its first break into the European market. Alex and Lou continue to study and prepare, seeing that they have a hard task in front of them if they are to reform the entire manufacturing division.