Goldratt uses his book to introduce his Theory of Constraints: a novel way to understand and structure complex systems so that they run smoothly. In Alex’s manufacturing plant, every piece of every product they make must go through several consecutive stages of shaping, molding, and cutting in various machines before becoming a final product. However, so many different machines are involved that the plant struggles to keep a steady workflow—some machines always have a backlog of parts to get through, while other machines wait empty and idle, causing delays and an unpredictable pace for every subsequent stage of the manufacturing process. To solve this problem, Jonah (who represents Goldratt) teaches Alex that in order to optimize any multi-stage process like a manufacturing plant, one must identify the system’s “constraints” or “bottlenecks”—the slowest stages of a process, which delay everything else—and then organize the entire system to work within the limits of those constraints.
Although every machine in the plant seems to cause delays, Jonah helps Alex to see that despite the plant’s complexity, it only has two true bottlenecks that cannot be sped up. This suggests that in any complex system, there will be a relatively small number of actual constraints that slow the whole thing down. Since delays randomly occur at every machine, Alex thinks that all of those problems could not possibly be tied to one or two bottlenecks in their manufacturing process. However, with Jonah’s help, Alex and his staff discover that whenever their process is delayed, the problem can be traced back to two vital but slow machines that are used for almost every product. Every other machine can work faster or adapt, but the bottleneck machines cannot. Since there is no alternative to either machine, whenever they are inactive and waiting for parts, their inactivity causes a chain reaction of delays throughout the rest of the manufacturing process. Everything slows down as a result of those two machines, making them the system’s bottlenecks, or constraints. Rather than a myriad of small issues, the plant struggles because of only two machines, suggesting that even in a complex system, the true number of constraints will be surprisingly small. Alex sees a version of this bottleneck effect during a hiking trip with his son, Dave’s, Boy Scout troop. As the boys hike single-file, Alex realizes that rather than hiking as a group, the hikers spread out along the trail: the fastest kids race ahead while the slowest, Herbie, languishes behind, representing the group’s bottleneck. Periodically, the others must stop and wait for Herbie to catch up, then start again and rebuild their momentum, causing their average hiking speed to be slower than the pace at which any of the boys would normally walk. Alex realizes that just as his manufacturing plant is thrown off pace—and thus, slowed down—by only two slow machines, so do the hikers struggle to maintain a steady pace due to one slow child, again suggesting that most systems are actually limited by a small number of constraints.
Alex realizes that by letting the bottlenecks set the pace for the entire manufacturing process, he can ensure that the bottlenecks are always running at maximum speed and the plant can maintain its peak production level, suggesting that one should prioritize their constraints rather than ignore them. In the manufacturing plant, Jonah advises Alex that by letting the bottlenecks set the pace of the entire plant, the two slowest machines will always be working at their full capacity. Although some other machines might be idle while waiting for the bottlenecks, as long as the bottlenecks are always running and never idle, the plant will already be making products as fast as it physically can. When Alex follows Jonah’s advice, although some machines are not always operating, the plant maintains a more consistent pace than ever before. Thus, it has an overall faster rate of production, since there are no more delays caused by disorder or starting and stopping. Alex sees this effect during the Boy Scout hike, too: when he places Herbie at the front of the group and the fastest hikers in the rear, everyone can easily maintain the pace set by Herbie. Rather than spreading out all over the trail, the hikers stay together as a group, eliminating all the time they previously had to waste regrouping and making sure everyone was still accounted for. This demonstrates that by letting the slowest member of a group (the bottleneck) set the pace, the overall pace of that group will increase, as there is less time wasted on reorganizing or course-correcting, which causes delays.
With his entire manufacturing system running at an even, organized pace, Alex can see the whole process clearly enough to find subtle ways to speed up the bottlenecks as well. This suggests that by working within the Theory of Constraints, one can keep their system organized and predictable, giving them a clearer understanding of their true constraints and possible solutions. With the manufacturing plant newly organized, productive, and predictable due to its steady pace, Alex and his staff realize that even their bottleneck machines can be slightly improved. They find faster ways to move products through the slowest machines that slightly lessens the bottleneck effect, allowing them to quicken the plant’s pace and make more products and more money. Similarly, after learning to hike as a group, the Boy Scouts realize that Herbie is loaded down by his overly-heavy pack and offer to carry some of his gear for him, which lets him hike a faster and allows the whole group to quicken their pace. In each instance, both the hikers and the manufacturing plant are able to organize themselves and even lessen the natural constraints that they must deal with, which increases their capabilities. Goldratt’s theory ultimately shows that leaders should recognize their constraints and make them the factor that paces an entire system, which will thus optimize that system’s output.
Working with Constraints ThemeTracker
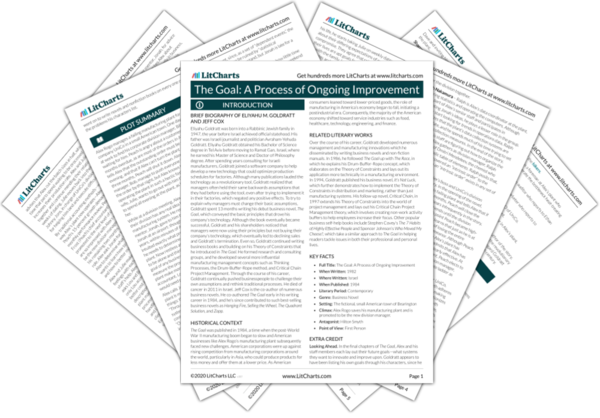
Working with Constraints Quotes in The Goal: A Process of Ongoing Improvement
Our hike is a set of dependent events…in combination with statistical fluctuations. Each of us is fluctuating in speed, faster and slower. But the ability to go faster than average is restricted. It depends upon all the others ahead of me in line. So even if I could walk five miles per hour, I couldn’t do it if the boy in front of me could only walk two miles per hour. And even if the kid directly in front of me could walk that fast, neither of us could do it unless all the boys in the line were moving at five miles per hour at the same time.
Unlock explanations and citation info for this and every other The Goal: A Process of Ongoing Improvement quote.
Plus so much more...
Get LitCharts A+“This much is clear to me. We have to change the way we think about production capacity. We cannot measure the capacity of a resource in isolation. Its true productive capacity depends upon where it is in the plant. And trying to level capacity with demand to minimize expenses has really screwed us up. We shouldn’t be trying to do that at all.”
“A bottleneck […] is any resource whose capacity is qual to or less than the demand placed upon it. And a non-bottleneck is any resource whose capacity is greater than the demand placed upon it.”
“I’m going to have Bob Donovan put together an I.E. to write up [your new] procedures formally, so we can start using them round the clock. […] You keep that mind of yours working. We need it.”
“But what are we supposed to do?” asks Bob. “If we don’t keep our people working, we’ll have idle time, and idle time will lower our efficiencies.”
“So what?” asks Jonah. […] “Take a look at the monster you’ve made. It did not create itself. You have created this mountain of inventory with your own decisions. And why? Because of the wrong assumption that you must make the workers produce 100 percent of the time, or else get rid of them to ‘save’ money.”
“If we don’t go ahead with a system to withhold inventory and release it according to the bottlenecks, we’ll be missing a major opportunity to improve performance and save the plant. And I’m not about to stand by and let that happen just to maintain a standard that obviously has more impact on middle management politics than it does on the bottom line. I say we go ahead with this. And if efficiencies drop, let them.”
“It’s perfectly okay to have more setups on non-bottlenecks, because all we’re doing is cutting into time the machines would spend being idle. Saving setups at a non-bottleneck doesn’t make the system one bit more productive.”
“Things start to be connected to each other. Things that we never thought were related start to be strongly connected to each other. One single common cause is the reason for a very large spectrum of different effects. You know Julie, it’s like order is built out of chaos. What can be more beautiful than that?”